People and Process: Empowering Employees and Integrating Technology
Industry leaders should be optimizing their technology, production and distribution capacity to ensure employee safety
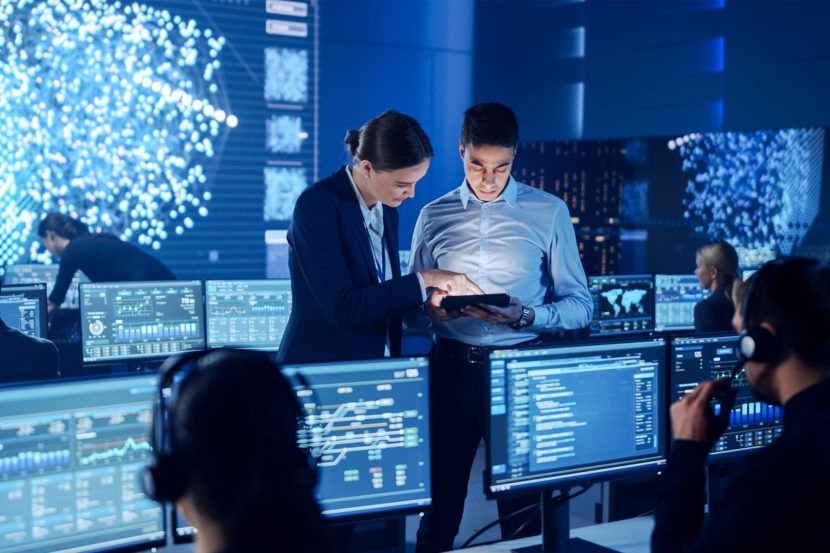
2020, for many business leaders, will be remembered as the year in which the fragility of the global supply chain was laid bare. The onset of Covid-19 early in the year and the impact that this had at the core of GVC hubs such as China, Europe and the US has sent ripples across supply networks worldwide and consequently, the scrutiny that the supply network is under within the modern business has never been higher.
We live in uncertain times subject to certain change and as such there has never been a greater opportunity for executives to iterate and question their existing supply chain infrastructure & focus.
By effectively redefining industry 4.0 via technology, convergence & prioritization for smarter supply, managing people and process by empowering employees and integrating technology and revolutionizing the last mile with disruptors, logistics and optimization, supply chains can more efficiently shield themselves from the looming threat, whilst moving towards the future and beyond.
People, Process, Technology
Covid-19 has obviously been detrimental to both the mental and physical wellbeing of supply, procurement and logistics staff and so naturally employers should be searching for the innovative means of protecting these individuals from harm, a pursuit that will pay dividends in the long-run. Currently, the critical issues relating to people and process are twofold.
Health & Safety
As supply chains evolve with the influence of technological innovation and transformation, the question of what happens to the health and safety of the workers affected by these developments is brought to the forefront as actions taken in one part of the supply chain can adversely (or beneficially) affect those on the receiving end of them. Typically, suppliers have had to worry about more obvious health and safety risks, such as manual handling and occupational health, Covid-19 has forced suppliers to adapt.
Industry leaders should be optimizing their production and distribution capacity to ensure employee safety, such as by supplying personal protective equipment and engaging with communication teams to share infection-risk levels and work-from-home options. These steps will enable leaders to understand current and projected capacity levels in both workforce and materials, as well as educate their staff on the importance of Covid compliance.
The Skills Gap
As stated above, the supply chain is experiencing a technological evolution. with disruption led by the Internet of Things, Artificial Intelligence and Blockchain likely to alter supply chains in coming years. All of these innovations are important in improving the day-to-day operations of employees, but technology is only as groundbreaking as those that wield it and, to that end, the widening skills gap amongst supply chain workers has become a real issue.
According to Accenture Strategy research, more than four in five supply chain executives (87%) believe that digital advances will drive major changes in the supply chain job mix over the next three years, it is likely that more staff will be employed to help the digitization process described above. Digital technology like artificial intelligence (AI), robotics and predictive analytics is becoming commonplace, the future supply chain workforce will need people who are highly engaged with digital process.
How Does Managing ‘People and Process: Empowering Employees and Integrating Technology’ Help Your Business?
- Aids in the development of a refreshed digitally driven procurement operating model
- Helps to innovate with purpose
- Increases resiliency across the supply chain and its territories
- More readily able to leverage digital capabilities
- Keep the planning workforce healthy and productive by supporting new ways of working
However, this is just one of the three key solutions mentioned above that a supply chain might employ to quickly respond to the threat posed by the coronavirus whilst also future-proofing their business for years to come.
To learn more, download the full report here or continue the debate at NG Supply Chain Summit NA, a GDS Summit, where we bring together senior supply chain executives who are actively seeking to share, learn, engage, and find the best technology solutions.
GDS Group hosts experts to help experts. We strive to provide an atmosphere for our attendees that enables them to confidently lead their companies through major transformation projects. For information on upcoming events, view our view our Digital Summits. To remain current on our activities, visit GDS Group on LinkedIn | Facebook | Twitter.